Qiang Hong, Ph.D.
Senior Research Scientist, Transportation Systems Analysis Group
Center for Automotive Research
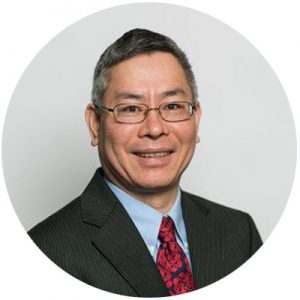
Dr. Qiang Hong’s research focused on the planning and policy implications of transformative automotive and transportation technologies, including connected and automated vehicles. His research also included personal mobility trends, automotive industry development, and transportation impacts in China. Qiang served as project panel member and chair of the Transportation Research Board (TRB) and the National Science Foundation (NSF).
Prior to joining CAR, Qiang was employed by Southern California Association of Governments (SCAG) and Southeast Michigan Council of Governments (SEMCOG). His responsibilities included developing regional transportation plans and providing technical support of modeling and policy analysis in both agencies. He was a principal planner at Beijing Municipal Institute of Urban Planning and Design, where he managed a variety of regional growth and transportation development projects.
Qiang received his Ph.D. in urban, technological, and environmental planning from the University of Michigan, Ann Arbor, and his M.Sc. in urban and regional planning and B.E. in architectural engineering from Tsinghua University, China.
Publications
- MDOT Processes in Connected and Automated Vehicle Environment
- Economic Evaluation of Commercial Remote Sensors for Bridge Health Monitoring
- Challenges and Opportunities for Developing Sustainable Transportation Systems in Beijing
- ITS Data Ethics in the Public Sector
- Management Procedures for Data Collected via ITS
- Global Harmonization of Connected Vehicle Communication Standards
- Use of ITS Technology for Management of Freight and Transit Assets
- Ethics of Government Use of Data Collected Via Intelligent Transportation Systems
- Pavement Condition Monitoring with Connected Vehicle Data
- Use of Data from Connected and Automated Vehicles for Travel Demand Modeling
- Connected vs. Automated Vehicles as Generators of Useful Data